PRODUCTS
Butterfly Valve
Ball Valve
Gate Valve
Globe Valve
Check Valve
Marine valve
Forged Steel Valve
Others
DIN Lift Check Valve
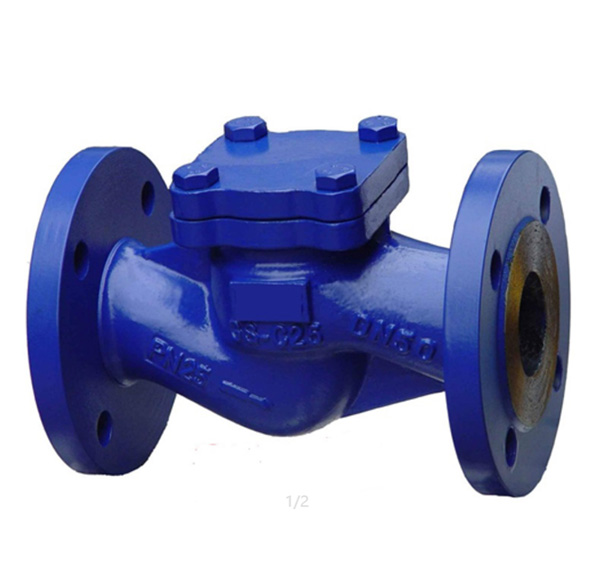
Short Description
Check valves are also known as counterflow valves, check valves, back pressure valves, and check valves. This type of valve is automatically opened and closed by the force generated by the flow of the medium itself in the pipeline, and is an automati..
Tags:Check Valve,Valve
Print this page
E-mail Us
Bookmark This
Skype Me
Quick Detail
DIN lift check valve is selected for pipelines of various working conditions such as petroleum, chemical, thermal power stations with a nominal pressure of PN1.6 to 6.4 MPa and an operating temperature of -29 to 550 °C. Applicable medium: water, oil, steam, etc.
Check valves are also known as counterflow valves, check valves, back pressure valves, and check valves. This type of valve is automatically opened and closed by the force generated by the flow of the medium itself in the pipeline, and is an automatic valve. The check valve is used in the piping system and its main function is to prevent backflow of the medium, prevent the pump and its drive motor from reversing, and discharge the medium in the container. The check valve can also be used to supply a supply line to an auxiliary system where the pressure may rise above the main system pressure.
Structure and characteristics
1. The materials are selected to meet the relevant domestic and foreign standards, and the overall quality of the materials is high.
2. The sealing pair is advanced and reasonable. The sealing surface of the valve disc and the valve seat is made of iron-based alloy or Stellite cobalt-based hard alloy surfacing surface. It is wear-resistant, high-temperature resistant, corrosion-resistant and scratch-resistant. long life.
3. The products are designed and manufactured according to the national standard GB/T12235.
4. Various pipe flange standards and flange seal types can be used to meet various engineering needs and user requirements.
5.The valve body material is complete, the gasket can be reasonably matched according to the actual working conditions or user requirements, and can be applied to various pressure, temperature and medium working conditions.
The check valve can be designed and manufactured according to user requirements and can be used for various equipments.
Main size and weight
PN | DN | L | D | D1 | D2 | b | n-Φd | H | W(kg) |
---|---|---|---|---|---|---|---|---|---|
1.6MPa | 15 | 130 | 95 | 65 | 45 | 14 | 4-14 | 58 | 2.0 |
20 | 150 | 105 | 75 | 55 | 14 | 4-14 | 63 | 2.7 | |
25 | 160 | 115 | 85 | 65 | 14 | 4-14 | 71 | 3.5 | |
32 | 180 | 135 | 100 | 78 | 16 | 4-18 | 84 | 5.4 | |
40 | 200 | 145 | 110 | 85 | 16 | 4-18 | 96 | 6.5 | |
50 | 230 | 160 | 125 | 100 | 16 | 4-18 | 115 | 9.1 | |
65 | 290 | 180 | 145 | 120 | 18 | 4-18 | 145 | 14 | |
80 | 310 | 195 | 160 | 135 | 20 | 8-18 | 156 | 25 | |
100 | 350 | 215 | 180 | 155 | 20 | 8-18 | 170 | 40 | |
125 | 400 | 245 | 210 | 185 | 22 | 8-18 | 201 | 56 | |
150 | 480 | 280 | 240 | 210 | 24 | 8-23 | 238 | 90 | |
2.5MPa | 15 | 130 | 95 | 65 | 45 | 16 | 4-14 | 60 | 4 |
20 | 150 | 105 | 75 | 55 | 16 | 4-14 | 64 | 5 | |
25 | 160 | 115 | 85 | 65 | 16 | 4-14 | 68 | 6 | |
32 | 180 | 135 | 100 | 78 | 18 | 4-18 | 79 | 9 | |
40 | 200 | 145 | 110 | 85 | 18 | 4-18 | 98 | 12 | |
50 | 230 | 160 | 125 | 100 | 20 | 4-18 | 110 | 16 | |
65 | 290 | 180 | 145 | 120 | 22 | 8-18 | 160 | 24 | |
80 | 310 | 195 | 160 | 135 | 22 | 8-18 | 170 | 31 | |
100 | 350 | 230 | 190 | 160 | 24 | 8-23 | 195 | 45 | |
125 | 400 | 270 | 220 | 188 | 28 | 8-25 | 225 | 68 | |
150 | 480 | 300 | 250 | 210 | 30 | 8-25 | 255 | 100 |
Main size and weight
PN | DN | L | D | D1 | D2 | b | n-d | H | W(kg) |
---|---|---|---|---|---|---|---|---|---|
4.0MPa | 15 | 130 | 95 | 65 | 40 | 16 | 4-14 | 100 | 4 |
20 | 150 | 105 | 75 | 51 | 16 | 4-14 | 105 | 5 | |
25 | 160 | 115 | 85 | 58 | 16 | 4-14 | 120 | 6 | |
32 | 180 | 135 | 100 | 66 | 18 | 4-18 | 130 | 9 | |
40 | 200 | 145 | 110 | 76 | 18 | 4-18 | 135 | 12 | |
50 | 230 | 160 | 125 | 88 | 20 | 4-18 | 149 | 15 | |
65 | 290 | 180 | 145 | 110 | 22 | 8-18 | 164 | 18 | |
80 | 310 | 195 | 160 | 121 | 22 | 8-18 | 169 | 25 | |
100 | 350 | 230 | 190 | 150 | 24 | 8-23 | 194 | 35 | |
125 | 400 | 270 | 220 | 176 | 28 | 8-25 | 225 | 65 | |
150 | 480 | 300 | 250 | 204 | 30 | 8-25 | 255 | 100 | |
6.4MPa | 15 | 210 | 105 | 75 | 40 | 18 | 4-14 | 100 | 7 |
20 | 230 | 125 | 90 | 51 | 20 | 4-18 | 110 | 11 | |
25 | 230 | 135 | 100 | 58 | 22 | 4-18 | 125 | 13 | |
32 | 260 | 150 | 110 | 66 | 24 | 4-23 | 152 | 14 | |
40 | 260 | 165 | 125 | 76 | 24 | 4-23 | 168 | 20 | |
50 | 300 | 175 | 135 | 88 | 26 | 4-23 | 170 | 23 | |
65 | 340 | 200 | 160 | 110 | 28 | 8-23 | 188 | 37 | |
80 | 380 | 210 | 170 | 121 | 30 | 8-23 | 205 | 46 | |
100 | 430 | 250 | 200 | 150 | 32 | 8-25 | 230 | 68 | |
125 | 500 | 295 | 240 | 176 | 36 | 8-30 | 245 | 93 | |
150 | 550 | 340 | 280 | 204 | 38 | 8-34 | 265 | 120 | |
10.0MPa | 15 | 210 | 105 | 75 | 40 | 20 | 4-14 | 100 | 7 |
20 | 230 | 125 | 90 | 51 | 22 | 4-18 | 110 | 11 | |
25 | 230 | 135 | 100 | 58 | 24 | 4-18 | 125 | 13 | |
32 | 260 | 150 | 110 | 66 | 24 | 4-23 | 140 | 14 | |
40 | 260 | 165 | 125 | 76 | 26 | 4-23 | 168 | 25 | |
50 | 300 | 195 | 145 | 88 | 28 | 4-25 | 170 | 28 | |
65 | 340 | 200 | 170 | 110 | 32 | 8-25 | 188 | 42 | |
80 | 380 | 230 | 180 | 121 | 34 | 8-25 | 205 | 65 | |
100 | 430 | 265 | 210 | 150 | 38 | 8-30 | 230 | 95 | |
125 | 500 | 310 | 250 | 176 | 42 | 8-34 | 245 | 115 | |
150 | 550 | 350 | 290 | 204 | 46 | 12-34 | 265 | 142 | |
16.0MPa | 32 | 260 | 165 | 115 | 85 | 30 | 4-25 | 170 | |
40 | 260 | 175 | 125 | 92 | 32 | 4-27 | 190 | ||
50 | 300 | 215 | 165 | 132 | 36 | 8-25 | 300 | ||
65 | 340 | 245 | 190 | 152 | 44 | 8-30 | 300 | ||
80 | 380 | 260 | 205 | 168 | 46 | 8-30 | 370 | ||
100 | 430 | 300 | 240 | 200 | 48 | 8-34 | 410 |